Harley-Davidson Partners with Protolabs for Part Changes That Win Races
Sep 27, 2024
Harley-Davidson Partners with Protolabs for Part Changes That Win Races
The Harley-Davidson Factory Racing (HDFR) team is partnering with Protolabs during its 14-race season. Protolabs helps to prototype, test, learn, iterate, and order final parts for the 620-pound Road Glide motorcycles. All the work had to be completed between races – before the green flag drops the following weekend.
After each race, HDFR collects first-hand feedback from the racers. They combine that feedback with quantitative data that analyzes performance in every straightaway and turn. Based on the feedback and data, HDFR engineers quickly iterate changes to the parts using Protolabs.
The team competes in the King of the Baggers series, a one-of-a-kind motorcycle competition that brings together the best riders in the world to race large Harley-Davidson Road Glide motorcycles breakneck speeds. The racing team’s dedication to constant iteration has produced faster, nimbler bikes capable of setting course records at each stop throughout the race season.
A partnership built on speed and quality
Combining Harley-Davidson Factory Racing’s engineering team with Protolabs’ digital manufacturing expertise has allowed the team to take lessons learned from a Sunday race and translate that knowledge into a new part design. During the ensuing week, the team can re-do the final part using a race-ready lightweight material. This process delivers significant year-over-year improvements in race times, and that has resulted in podium wins for riders Kyle Wyman and James Rispoli.
Related:NASA and Protolabs Demonstrate the Value of Generative Design
To achieve superior performance, the team needs revamp parts quickly. “For us to be successful in the King of the Baggers series, we need to respond rapidly to what we are learning on the racetrack, and to do that we require a partner that is able to bring these ideas to life,” said Jason Kehl, HDFR principal. “As a digital manufacturer, Protolabs allows us to make those weekly incremental improvements that lead to season-long success.”
3D-printed exhaust translates to tight turns on the track
HDFR engineers constantly evaluate how they can modify parts on the bike to spike performance. As an example, tight turns on the track are pivotal to HDFR’s success. An extra lean angle can improve performance and deliver comfort for the rider. Just one-half degree of extra lean angle during turns can reduce track time by about 1/10 of a second. With some racetracks sporting as many as 14 turns in a single lap, the benefits of increased lean angle are clear.
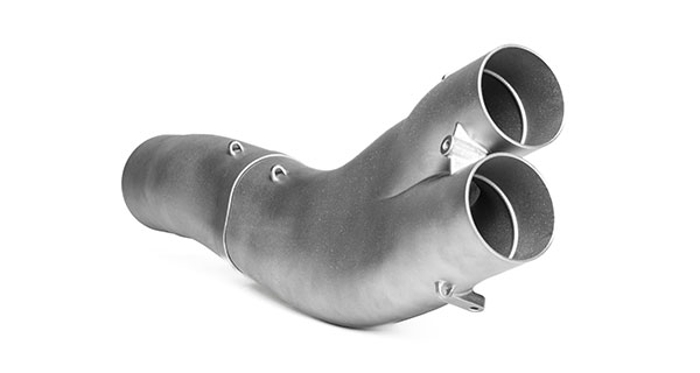
The DMLS-printed exhaust utilized titanium for a lightweight, organic design. Image courtesy of Protolabs.
The exhaust components on the right side of the motorcycle offered the best potential for improving lean angle, so the team turned to the design freedom of metal 3D printing at Protolabs to see what is possible. The result was an organically designed exhaust that tucks in closer to the bike, ultimately allowing Wyman and Rispoli to ride closer to the ground on right-hand turns.
Related:Swing a Leg over the Harley-Davidson LiveWire S2 Del Mar
A new video series highlights Harley-Davidson’s success and its critical manufacturing partnership with Protolabs.