A Novel Vision for 3D Printing
Sep 10, 2024
A Novel Vision for 3D Printing
Many approaches to additive manufacturing have been inspired by conventional printing processes—hence the common term, 3D printing. Inkbit’s approach to 3D printing, however, takes that inspiration a bit further.
“Just like an ink-jet printer can print different colors, we can print with different materials and hardnesses in a single part or assembly,” Javier Ramos, Inkbit’s cofounder and chief technology officer, tells Design News. The company’s method deposits each layer by jetting roughly 63 million droplets of polymer material (or multiple materials contemporaneously) about 20 to 40 microns thick and cures it using UV light. Each printed layer is then inspected through AI-enabled high-speed scanning, and the process repeats, layer by layer.
Inkbit calls its method Vision-Controlled Jetting (VCJ). The digitally controlled inspection process does not require contact with the printed material, which makes it different from legacy systems that use mechanical elements like rollers. Those systems can “impose limits on materials and disturb shapes,” he says. “VCJ enables better, more accurate parts and allows the use of a wider spectrum of chemistries. It also supports printing of complex lattice and foam structures that are difficult or impossible to produce with DLP, SLA, or powder technologies.”
The company uses a wax support material during the printing process that can be recycled. “It is inexpensive and easy to remove with heat—it just drains away,” he explains. “Wax has low viscosity, so it is easy to clean in post-processing. Others use water jetting, but it can be difficult to clean channels with it."
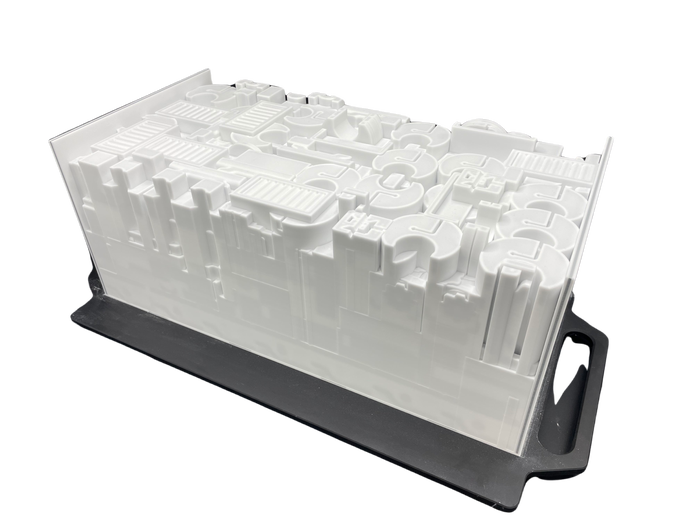
The wax support material surrounding printed parts. INKBIT
Inkbit develops its own materials and offers a family of thermoset polyurethanes (TEPUs) as well as a family of epoxy materials. It also develops entirely new chemistries in partnership with customers, to fit their needs more accurately.
“Our combination of printing, materials, and scanning can achieve very fine and precise channels and holes,” Ramos says. “We can print very unique parts with nearly limitless design possibilities.”
Check out the below video to see Inkbit's technology in action.
Applications for multimaterial 3D printing
Inkbit’s proprietary materials as well as its ability to print different materials in one part or assembly has enabled the company to tap into a range of applications. Elastomeric uses include gaskets, sealing O-rings, and suction cups. Foams can be printed to provide cushioning or haptic properties, and other applications include thermal and mechanical insulation foams.
“For some applications, our materials could replace traditional rubbers and foams such as EPDM and BUNA as well as polyurethanes and silicones,” he says. And because its additive manufacturing process doesn’t require expensive molds, the company has been “producing elastomer gaskets in a matter of days, allowing engineers to design solutions more optimally."
Functional parts can also be printed. “There’s a lot of companies that print rigid parts. We see an opportunity for elastomeric and multimaterial parts,” Ramos continues. “Multimaterials can be bonded, integrated, or free-floating, giving engineers geometric freedom.”
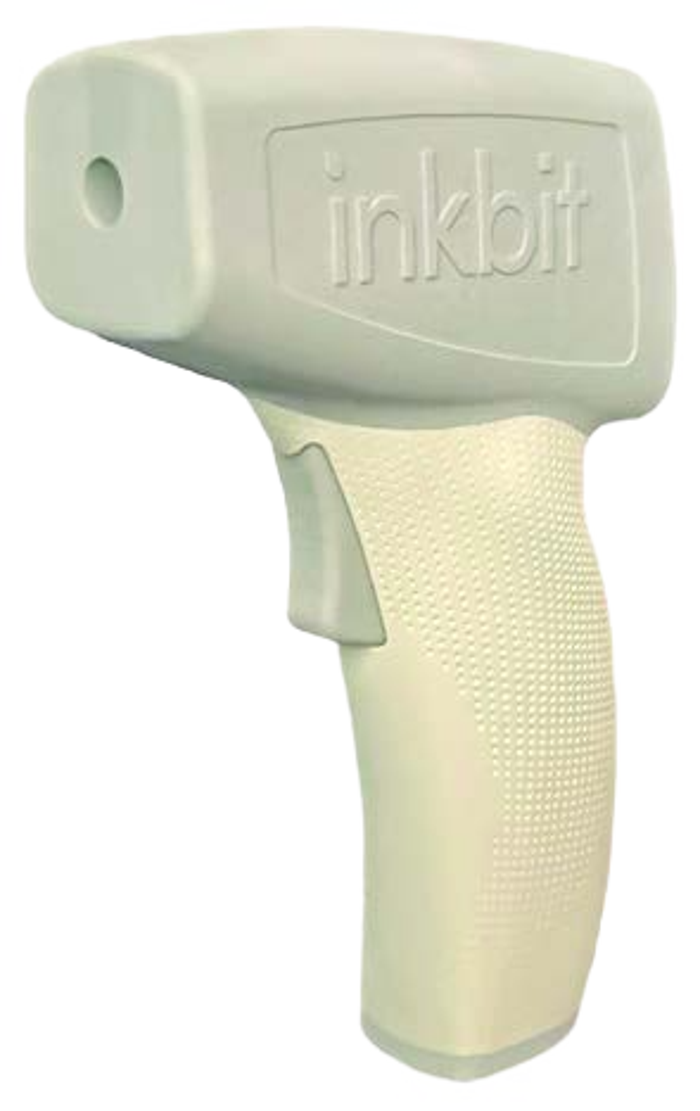
Single-printed, multi-material part using both rigid and elastomer materials. INKBIT
The company can provide equipment (called Inkbit Vista) and materials or can print parts for customers through its “digital factory.” “We can review designs, print, and provide QA/QC and parts delivery,” he adds. “We also offer application engineering services. We are very commercially flexible and offer a team of chemists, hardware, and process engineers to optimize our core tech for customer requirements.”
Inkbit also partners with customers to develop solutions for specific applications. “We are open to collaboration in design and engineering,” he says. “We are partnering with a customer on developing a specific dental application and with another customer on developing industrial flow control components. We have the ability to modify and develop new materials, hardware, and software to enable new applications.”
The company has even been tackling some of the digital challenges of additive manufacturing. “One bottleneck is that files sizes are huge,” Ramos explains. “People spend hours designing and managing files. We have developed a fully integrated CAD-to-print workflow that eliminates the need to work with large STL files. Construct, our build preparation tool, enables the design of complex foams and multi-material parts that can be printed directly on our Vista system without exporting large STL files. This saves our users time and removes a lot of frustration from the part design and build preparation process.”
As much as Inkbit has already demonstrated in terms of technology, Ramos says the company is still in “an exploration phase and engaging with a lot of different customers. We are playing in both prototyping and end-use production. We aim to accelerate innovation and development.”