Spin Cycle: Stainless Steel Sets the Standard for Dishwasher Circularity
Nov 13, 2024
Spin Cycle: Stainless Steel Sets the Standard for Dishwasher Circularity
Household appliances and how we use them have a greater impact on our environment than we might think. The Collaborative Labeling and Appliance Standards Program (CLASP) estimates that appliances account for nearly 40% of all global energy-related CO2 emissions. At every phase of an appliance’s lifecycle, from production to recycling, early design and material selection decisions have a cumulative carbon impact, especially as condition deteriorates.
As buyers turn to more-sustainable products in their households, and especially those buyers who are always on the lookout for something “premium,” the pressure is on for appliance manufacturers to design goods that are increasingly energy- and resource-efficient. The home appliance sector is already making great progress in this respect—but it can go further by adopting a circular economy model. A good starting point is to examine the sources of the raw materials it uses to manufacture its products.
Slashing carbon emissions
Switzerland’s leading brand in household appliances, V-ZUG, considers creating energy efficient appliances to be a crucial aspect of sustainability. They’ve cut energy and water use in their machines, such as the AdoraDish V6000 dishwasher, which features a heat pump to save 30% energy compared with conventional dishwashers by recovering wastewater heat. Additionally, it reuses rinsing water in the next cycle, conserving the energy and natural resources needed for water treatment.
Related:New Metalworking Solutions for Automotive Interiors
The producer has already reached carbon neutrality across its production sites by implementing measures such as decarbonizing heating systems, updating logistic fleets, and switching to renewable energy. The next challenge they face is addressing the CO₂ emissions embedded in the raw materials they source.
Much more needs to be considered throughout the entire lifecycle of the appliance—from procurement, development, and manufacturing to service, reuse, and recycling. They believe that strong and innovative partnerships are critical to further reducing the carbon footprint of their products. This is where sustainable stainless steel comes in.

V-ZUG
Circle Green
As a long-time customer and partner of Outokumpu, V-ZUG quickly responded when we introduced our towards-zero stainless steel, Outokumpu Circle Green.
From a metallurgical perspective, Circle Green stainless steels are identical to existing market products. They offer the same performance and mechanical behavior during their life cycle and production. The key difference is that Circle Green production involves stringent controls to minimize emissions at every stage—from sourcing and manufacturing to processing and logistics. This results in a carbon footprint up to 93% lower than the global average.
V-ZUG saw this as an opportunity to reduce the environmental impact of its products without altering their design or production processes.
Beginning discussions in early 2023, V-ZUG decided to incorporate Circle Green stainless steel into its Adora dishwasher, receiving its first shipment in June. The first appliances featuring this material were delivered to customers in September 2023. Now, Circle Green is the standard material for key components in the machine’s main compartment.
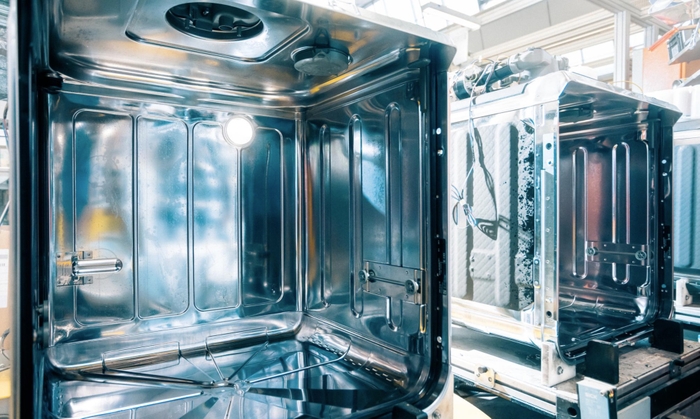
V-ZUG
A low-carbon future
Outokumpu uses steel scrap suppliers, but it also sources recyclable material from its own production waste streams. Circle Green, which is primarily made from the latter, originates from Outokumpu Tornio mill, in Finland—one of Europe's largest recycling centers. From Tornio, the coils are sent to Germany for additional processing before reaching Zug in Switzerland. In Zug, V-ZUG develops and manufactures many of its products.
Outokumpu Circle Green is achieved using renewable and low-carbon energy forms, up to 100% recycled raw materials and reinvented production processes.
Circle Green supports a sustainable transition across multiple industries, including the home appliance sector. V-ZUG’s current CO₂ intensity, at 1.8 kg CO₂e per tonne of stainless steel, is already much lower than the industry average of 7 kg CO₂e per tonne. With Circle Green, there is potential to reduce this even further, to 0.5 kg CO₂e.
By adopting and investing in more sustainable technologies and materials like Circle Green, companies can play a key role in mitigating the effects of climate change while appealing to an audience of increasingly sustainability-conscious buyers. The desire to credentialize brands via the use of low-emissions materials is stronger than ever—and for dishwashers, stainless steel is the ideal solution.
For more information visit www.outokumpu.com.